“Today, EHS practitioners continue to rely on injury rates, absenteeism, and other lagging metrics despite the growing acceptance of the fact that these failure-focused measures are ineffective in driving continuous improvement efforts. Leading indicators, on the other hand, appear to offer a more useful gauge of EHS activity by providing early warning signs of potential failure and, thus, enabling organizations to identify and correct deficiencies before they mature into accidents and injuries.”
— Campbell Institute, Transforming EHS Performance Measurement Through Leading Indicators
Striking the balance between lagging and leading indicators
We’re in the midst of an EHS transformation — and the good news is that the speed of it is in good shape. Just like the shifting mindset from safety work to safety of work, the way EHS professionals approach safety indicators has come a long way.
With their long history of use, lagging indicators have been valuable for identifying trends in past performance and have become an accepted benchmark standard both within and across industries. Yet, lagging indicators tell just one part of your safety story.
When observing a low injury rate, managers might grow complacent, relegating safety to the bottom of their priorities. However, this perception overlooks the numerous workplace risk factors that could potentially lead to future injuries, illnesses, or fatalities.
On the other hand, leading safety indicators measure events leading up to injuries, illnesses, and other incidents, allowing you to forecast potential risks in your safety and health program.
Achieving a balance between leading and lagging indicators is essential, yet only 27.8% of organizations have managed to do so.
To grasp what lies ahead, it is crucial to comprehend the obstacles that have prevented safety teams from genuinely transforming EHS with leading indicators, specifically the challenge of scaling and operationalizing these indicators in their day-to-day tasks.
The burden of administrative tasks
Done right, your EHS data enables corrective actions in your safety operations and puts you in a position to mitigate risks effectively. However, a typical day for EHS teams is becoming overwhelmed with administrative tasks — between conducting inspections and audits and reporting incidents. Furthermore, scrambling to derive meaningful insights from disjointed data hampers EHS teams' ability to focus on which risks they should prioritize, creating barriers in decision-making processes.
Additionally, the administrative burden in EHS prevents safety teams from taking a unified view of their safety performance. This leads to disjointed data that is not actionable on its own and focuses solely on ensuring regulatory compliance. Managing huge amounts of administrative resources to collect data, diversifying workflows, and expanding teams without sacrificing performance are not a piece of cake.
Highly successful EHS transformations typically require scalability to adapt easily to the changing conditions of a facility, empowering the EHS team to gain a retrospective look at their safety performance based on lagging indicators. But the question of how to precisely identify areas within an EHS program that need improvement and to what extent inevitably leads us to dive deep into the leading indicators.
Top leading indicators to consider
Firms seeking to scale and operationalize leading indicators should consider OSHA’s recommended best practices to reach a more proactive safety approach based on historical data. Here are the OSHA’s recommended practices:
• Collect existing information about workplace hazards: Gather past records and data to identify existing hazards in the work environment.
• Inspect the workplace for safety hazards: Conduct regular inspections to detect potential safety risks in the workplace.
• Identify health hazards: Evaluate workplace conditions to uncover any factors that could negatively impact employee health and safety.
• Conduct incident investigations: Analyze past incidents to understand their root causes and prevent recurrence.
• Identify hazards associated with emergency and non-routine situations: Assess risks tied to unexpected or infrequent scenarios to enhance preparedness.
• Characterize the nature of identified hazards, identify interim control measures, and prioritize the hazards for control: Categorize hazards by severity, implement temporary safety measures, and focus on controlling the most critical risks first.
Since capturing leading safety indicators in real time requires high visibility into EHS operations, this task is almost impossible for EHS teams still working with traditional methods.
High volumes of data can hinder safety teams from focusing on the most critical risks and operations. Therefore, when selecting your leading indicators as suggested by OSHA, we recommend considering these three metrics that can be provided by AI-powered EHS management software.
Best practices to leverage leading safety indicators
Without a holistic view of these leading indicators, leveraging their predictive capabilities and taking meaningful corrective actions becomes quite challenging.
Fortunately, there are practices to follow that can transform leading indicators into truly useful tools. By applying these practices, you will not only effectively utilize leading indicators but also gain the ability to catalyze the transformation of your EHS operations.
Employ safety score
Your team consistently strives to enhance safety within your organization, dedicating considerable effort to implementation. However, the challenge lies not in executing these initiatives, but rather in quantifying their efficacy and conveying tangible results to higher management.
Like many safety teams, you likely encounter difficulties in this endeavor, despite conducting regular safety audits. While audits offer valuable insights, they often fail to paint a comprehensive picture or adequately tangibly showcase data.
Rather than solely relying on safety audit checklists, you can get a more nuanced portrayal of your data through a safety scorecard.
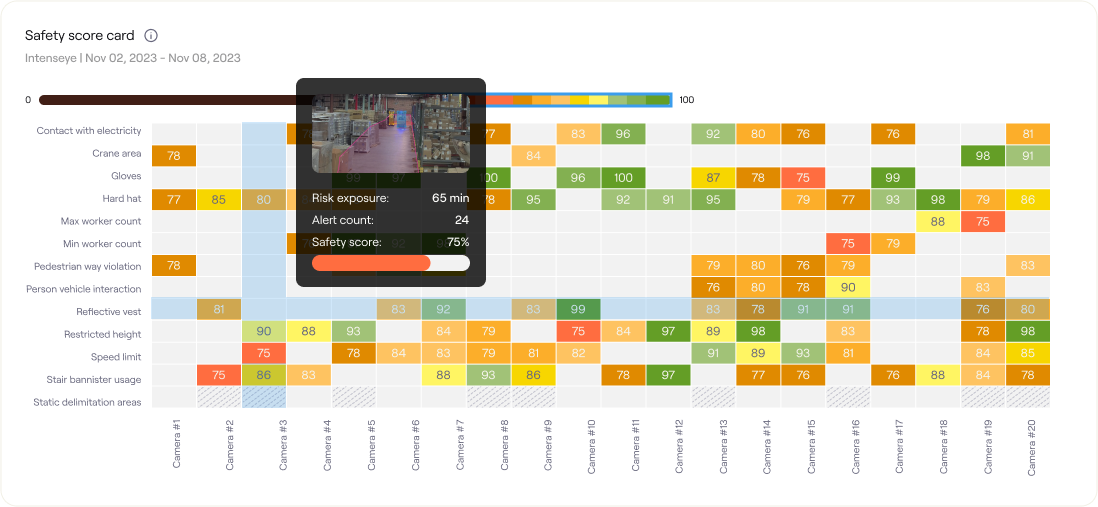
By actively tracking your safety performance, equip yourself with a safety scorecard that enables real-time tracking of progress. Whether it's assessing developments on a weekly, monthly, or yearly basis, this scorecard offers insights into your journey.
Moreover, scorecards surpass basic audit checklists by providing assessments that consider the spectrum of outcomes, moving beyond mere pass-fail evaluations.
Set SMART KPIs
Leading indicators show you which corrective actions you need to take, implying the establishment of a series of new targets. OSHA emphasizes the importance of setting SMART targets that are Specific, Measurable, Accountable, Reasonable, and Timely:
• Specific: Are your leading indicators specific enough to allow you to take corrective actions aimed at reducing safety hazards or indicating areas where improvements are needed?
• Measurable: Is your leading indicator quantifiable, represented by a number, rate, or percentage that enables the monitoring and assessment of safety trends over time?
• Accountable: Does your leading indicator track a relevant item aligned with your safety goals?
• Reasonable: Is the goal set for your leading indicator realistically attainable?
• Timely: Are you tracking your leading indicators frequently enough to detect significant trends within your preferred timeframe?
Use artificial intelligence
Perhaps the most important best practice is leveraging the power of AI: leading indicators go beyond reporting past events or near-misses. Hundreds of unsafe acts and conditions that occur daily can serve as leading indicators for EHS teams.
AI has the capacity to equip an EHS professional, who previously relied solely on observation and manual documentation, with the ability to capture leading indicators 24/7 and classify them based on duration, frequency, or severity.
AI-generated leading safety indicators in action
Intenseye's AI captures all safety risks and provides a comprehensive view of leading indicators. Organizations gain visibility into all their facilities through AI-generated leading indicators, which offer clear, quantifiable metrics based on the duration of risk exposure for unsafe acts and the frequency of unsafe conditions.
These metrics enable EHS professionals to measure and track safety performance over time, facilitating more data-driven and justified decision-making.
Heineken Mexico utilized Intenseye's artificial intelligence to establish a unified safety culture across all of its factories. By collecting unbiased leading indicators, our AI has empowered their EHS teams to streamline their task management processes, resulting in significant advancements in their safety performance.
The words of Miguel Ángel Aguilera Rodríguez, Heineken's Head of Supply Chain Digital & Technology, highlight the direct impact of Intenseye's AI-powered EHS management software:
“By equipping us with real-time insight into leading indicators, the platform helps us drive proactive improvements that mitigate risks facing our frontline teams”
Identify critical hazards before they turn into accidents
As we navigate through the landscape of EHS transformation in leading safety indicators, where progress is steadily gaining momentum, it becomes evident that achieving a scalable solution is paramount.
While the pace of our journey is promising, it's essential to recognize that true scalability requires more than just speed. It demands innovation, adaptability, and a forward-thinking approach to effectively address the evolving challenges of safety management.
At the forefront of this transformation is Intenseye's AI-powered EHS management software. Intenseye enables organizations to capture, analyze, and respond to leading safety indicators in real-time, providing actionable insights that drive continual improvement and proactive risk mitigation.
Through its advanced AI capabilities, Intenseye empowers EHS professionals to optimize processes, elevate safety standards, and safeguard frontline teams from potential hazards. To better understand how to leverage safety with Intenseye explore our Leading Indicators feature now!
Resources
• Alberta, Leading Indicators for Workplace Health and Safety: a user guide
• Campbell Institute, Transforming EHS performance measurement through leading indicators
• OSHA, Leading Indicators
• OSHA, Using Leading Indicators to Improve Safety and Health Outcomes
• University of Nottingham, Leading Safety
• Intenseye, A day in the life of an EHS manager